Shilpi Sen was solely a school-going woman when she misplaced her aunt to breast most cancers. Being up shut with the illness made her realise the psychological agony it places its sufferers via, she says.
“I used to look at not solely my aunt, but additionally my grandparents struggling. Their psychological and bodily agony was monumental,” Shilpi, now 44, remembers to The Higher India.
In 2015, whereas she was nonetheless working at Nuffic Neso concerned in branding and selling research within the Netherlands, throughout a brand new 12 months’s dinner she met Vikas Garg, 32, a cloth scientist. This assembly would ultimately result in the formation of her organisation Prayasta — a startup that goals to personalise mushy tissue implants and prostheses.
Launched in 2017, Prayasta focuses on growing expertise that may assist produce personalised mushy tissue implants. They lately developed the world’s first 3D printer for implant-grade silicone in collaboration with the Indian Institute of Science (IISc), Bengaluru.
“Whereas we have been speaking, we realised that we had an identical imaginative and prescient — we each needed to fill the hole between expertise and the healthcare area,” she notes.
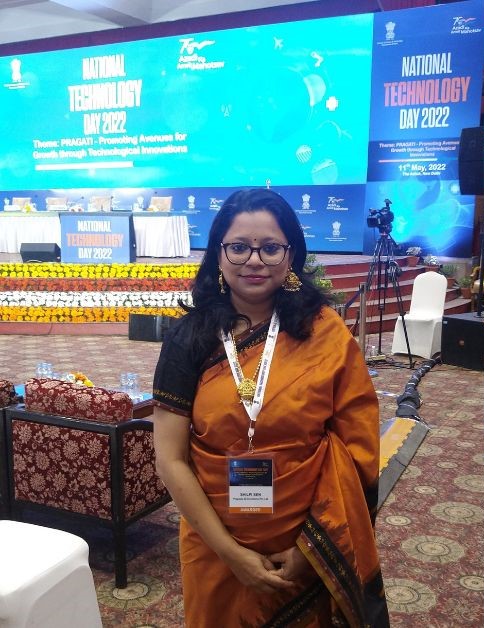
In the meantime, Vikas says that he was fascinated with mixing completely different supplies and amalgamating them with human our bodies, which is why he pursued a PhD in materials sciences. “l realised that I wish to apply the data reasonably than be on the analysis facet of issues. Academia is nice however at the moment it felt prefer it was not for me,” he says.
‘Personalisation — not a luxurious’
The duo say they observed there was no expertise that caters to the personalisation of sentimental tissue implants within the nation.
“When a lady is present process the surgical procedure, and the medical doctors realise that the brand new breast and the opposite breast are usually not of the identical dimensions, they do a surgical procedure on the wholesome breast to right the imbalance. That basically shook me. A lady who’s already a survivor and has seen sufficient goes via rounds of surgical procedure for no good purpose,” Shilpi laments.
Whereas such surgical procedures are painful procedures, an imbalance within the physique must be corrected.
“Statistically talking, your complete inhabitants will be categorised into say 10-20 sizes, however then each physique is barely completely different from one other. Each particular person’s physique is so distinctive. It isn’t solely true for breasts — take the instance of eyes, cheeks, or ears. Although personalisation would possibly sound like a luxurious, in such instances, it’s actually a necessity,” Vikas Garg, co-founder, Prayasta says.
He explains that the performance of the physique will depend on the implant. “Clinically talking, if a breast is absent from the physique, a considerable quantity of weight is absent. That offers rise to asymmetry. It’s a requirement that the burden of the physique stays balanced,” he says.
“In layman’s phrases, the trachea or the windpipe is only a pipe. However it isn’t a straight one. It’s rounded, someplace the contours are completely different. When somebody requires an answer for that — be it for most cancers or lung illness — if the match isn’t proper, the surgeon will find yourself making a smaller diameter trachea, resulting in leaks and restoration points. Therefore the necessity for personalisation,” Vikas explains.
The expertise
Suffering from the quite a few gaps within the implant trade and the assorted points sufferers undergo, the duo determined that they want an answer.
This led to the beginning of Silimac, the world’s first 3D printer for implant-grade silicone.
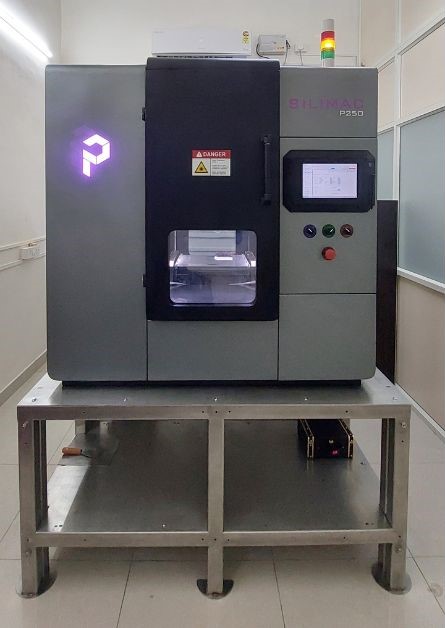
Silimac can straight 3D print implant-grade silicone materials to make an implant throughout the hospital itself. The implants will be personalised not solely when it comes to form, dimension, and contour, but additionally when it comes to weight, stiffness, contact and really feel, say the founders of Prayasta.
“We even have developed a expertise that we name NIA, or novel inner structure. It’s a plethora of designs that we use to fabricate personalised implants when it comes to form, dimension, contact, and weight. It’s liquidless, making it rupture-proof,” Shilpi explains.
“With this expertise we’re fixing three main issues — the difficulty of not having personalised implants, decreasing the danger of failure in surgical procedure, and making implants which can be appropriate for teenagers,” says Vikas.
He provides, “When children require options like this, they’re in a fragile and rising stage. So, the customisation of the implant must be much more exact.”
The 3D printer is now housed at IISc.
Dr Kaushik Chatterjee, affiliate professor, Division of Supplies Engineering and Centre for BioSystems Science and Engineering, IISc, says, “The sector of 3D printing is being adopted in a wide range of industries for a large spectrum of supplies, together with healthcare, amongst different purposes. Silicone is used as a alternative for mushy tissues within the physique however these are mass manufactured. Such implants don’t all the time match nicely to fulfill the anatomical wants of all sufferers. We at IISc are excited to companion with Prayasta to leverage this new expertise to supply patient-specific implants for improved scientific outcomes.”
Why silicone?
Silicone is a fancy materials, informs Vikas. It has a distinct chemical composition and isn’t very simple to print.
“We can’t take a traditional 3D printer and use silicone. Silicone is available in thousands and thousands of sorts, and we’re utilizing the implantable selection. The advantage of that is that silicone can keep within the physique for 10-15 years with none uncomfortable side effects to the physique,” he defined.
Implant-grade silicone is the very best biocompatible materials for human implants, which keep contained in the physique. There was a lot analysis on different supplies that can be utilized, however nothing is definite as of now, says Shilpi.
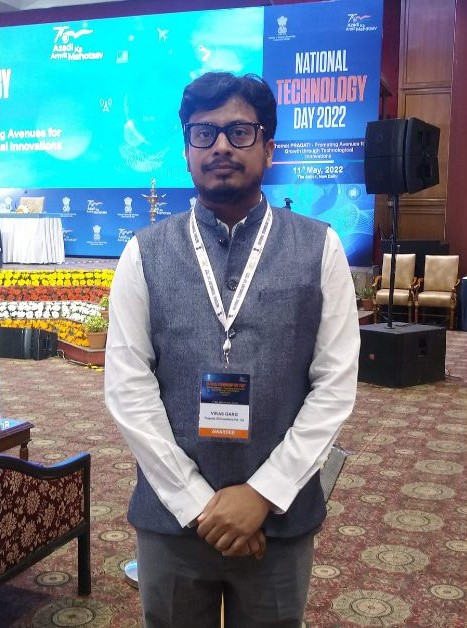
“One other drawback that this sort of implant solves is that at the moment, breast implants are like a balloon. There’s an outer shell of a skinny movie of silicone and inside can be silicone gel. The apparent danger is that there’s a danger of leakage, and if the gel is available in contact with the bloodstream, it may be deadly,” says Vikas.
By 3D printing implants with Silimac, this danger will get eradicated utterly, provides Vikas.
What’s subsequent for Prayasta?
Prayasta’s 3D printer is a one-of-a-kind, novel technology made by an Indian startup. Because the expertise is new, the price of manufacturing is excessive, says Shilpi.
“It’s unlucky that implant-grade silicone isn’t manufactured in India. So now we have to supply it from the US and Germany. The price of silicone is Rs 1 lakh per kg. Nonetheless, we wish to make it as reasonably priced as doable for everybody. Sooner or later, when the expertise is extra commercialised, then the affordability would possibly improve,” says Shilpi.
The co-founders say that they wish to take the expertise to the final mile.
“Now we have little or no management over the price of uncooked supplies. However we wish to make it as reasonably priced to everybody sooner or later, with investments from third events, as doable,” added Vikas.
Whereas the expertise is novel, IISc affiliate professor Dr Kaushik Chatterjee says, “This can be a cutting-edge expertise that has monumental potential for affected person care within the nation and worldwide.”
“We consider in shaping lives to be higher. We needed to do all the pieces from scratch because it was by no means executed earlier than. We wish to take it to international ranges and make personalised implants accessible to everybody, which is at the moment missing in our healthcare system,” says Shilpi.
Edited by Divya Sethu